|
|
Room Integrity Testing
|

|
|
Environmentally friendly
Fire fighting systems designed and produced by Gielle Fire Systems are renowned for their
reliability. However, there is a factor which is beyond the control of Gielle engineers that is one
of the most common causes for the failure of a system; the ‘Integrity’ of the protected room, i.e.
its capacity to hold gas.
Very little disruption
Prior to 1989 discharge testing was the only practical way to prove the ability of the protected
room to hold the gas. Today, the environmentally friendly option of Integrity Testing is the
accepted method. Both NFPA 2001 and 12A require an enclosure integrity test as part of the
acceptance procedure for all clean agent systems.
Does not interfere with extinguishing system
As well as being environmentally sound, Integrity Testing has several other advantages over the discharge test:
- It causes very little disruption to the working day, since unlike the discharge test, it does not require the tested area to be cleared, and the total expected running time of the test is approximately 4 hours
- The service is repeatable, allowing the room to be tested at any time, for example, if any changes are to be made to the protected area. It is recommended by the EPA, IRI, FM, other insurers, fire suppression equipment manufacturers and the FSSA that such tests should be repeated annually or after any building work.
- It is versatile. Neither the type of the gaseous fire fighting agent, nor the original provider of
the extinguishing system inhibits this vital service.
No system discharge required
Integrity Testing is vital, especially if as a company you have, or are due to decommission your
Halon system. New clean agents have less tolerance for leakage than Halon
systems. Halon protected rooms could lose over 50% of agent concentration before the fire could re-ignite. The
new agents are more critical and can normally only lose about 20% before re-ignition.
Therefore, what was an adequately sealed protected area for the use of Halon, would not be adequately
sealed for the use of a new agent. |
|
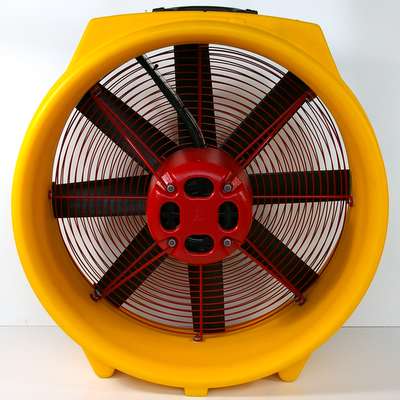
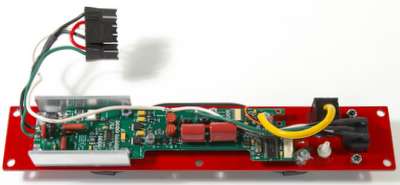
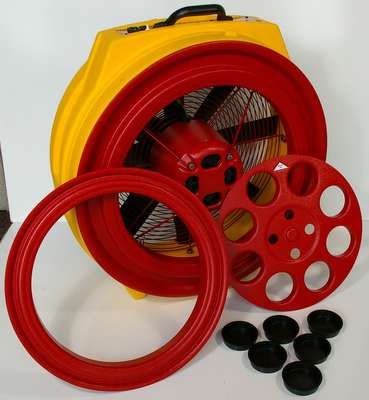 |
|
|
 |
|
|
|

|
|
HOW IT WORKS:
For any gaseous fire suppression installation to be effective, the design concentration must first be
achieved, and then maintained at suitable levels within the risk. In order to achieve this the protected area must be
adequately sealed around its boundary. Integrity Testing calculates the leak-tightness of a room and predicts
how long it takes for the interface between the extinguishing agent and the air to descend to a given
level.
The test equipment comprises of variable speed fans, expandable door panels, pressure gauges and a
dedicated portable computer. The door fan unit is fitted into a doorway of the protected area by means of the expandable door panels
designed to fit most door frame sizes, and measures the size of holes in the enclosure and the pressures
that may exist across them.
The fan speed is adjusted to obtain a steady pressure between the test area and the volume surrounding the
test area (equivalent to the column weight exerted by the extinguishing agent following a discharge). This
pressure is then maintained whilst readings are taken from pressure gauges.
The measured rate of air input needed to maintain this pressure level is equivalent to the amount leaking
from the test area. A second measurement is taken by doing the first test in reverse i.e. by de-pressurising
the test area. The two readings are averaged to reduce error.
The computer then converts the flow and pressure readings into an Equivalent Leakage Area (ELA), or the
total area of all the cracks, gaps and holes in the test area. The data generated is then processed using
specifically designed computer software, in compliance with the National Fire Protection Association
(NFPA) which predicts the period of time that the concentration will be held in the test area at a given
height. This retention time can be further calculated for different
heights.
The computer software has also been designed to be conservative with its predictions. The software
produces the worst case scenario in which 50% of the cracks, gaps and holes in the test area are at a low
level where heavier gas/air mixture will seep out and 50% are at a high level where lighter air will enter to
displace it. This approach makes the results extremely reliable and means that any system which passes the
room integrity test would have been virtually certain to pass a full discharge test.
Within an hour of the completed tests the computer produces a printout with full details of the input and test
results, with a detailed report following in the post shortly afterwards. Failure is indicated if it takes less than
ten minutes for the agent/air interface to drop below the minimum specified protected height. This minimum
holding time of ten minutes is the period suggested by BS5306 Section 5.1 and the
NFPA.
However, if the test area does fail to satisfy the requirements, a detailed survey is carried out making note of
the leakage areas to allow remedial sealing works to be carried out.
|
|

|
|

|
|
|
|
|